DFI MI P55-T36 + L3426 II 最終更新日 : 2020/05/23
|

去年の今頃は、INTEL D510MO、DFI P55-T36、ZOTAC H55-ITX、INTEL DH57JG等々、大忙しだった。その内、P55-T36とH55-ITXは、未だにまな板状態が続いている。
P55-T36はケースの作りかけ、H55-ITXはBIOSの更新待ち。そうこうする内にUbuntuやPT2に関心が移り、忘れた訳ではないが未完成のママ一年経ってしまった。 (2011.2.6)
|
|
L3426+Matrox M9120 (2011.2.6)
|

正月明けから作り始めたSandy Bridgeは、チップセットのリコール問題で暫く休戦することになった。 となれば、未完成のPCを仕上げる絶好のチャンスだ。よし、P55-T36にケリをつけよう。

そこで、P55-T36 + L3426 の部品一式を段ボール箱から取り出し「お盆」に据えた。ネジ一本に至るまで不足はなく、15分程度で再生した。部品構成は以下の通り。
【M/B】 DFI MI P55-T36
【CPU】 XEON L3426
【CPU Cooler】 Dynatron K129
【CPU Cooler Fan】 ENERMAX UCCL12
【MEM】 Patriot DDR3-1600 4GB×2
【VGA】 Matrox M9120 Plus LP PCIe x16
【SSD】 Intel X25-M 80GB
【HDD】 WD5000BEVT 500GB 5400rpm
【電源】 Silver Stone SST-ST45SF

?ヶ月ぶりに火を入れた結果は、
・動作に問題なし。
・Win7のUpdateも問題なし。
・CPUクーラーのファンを交換したので、BIOSのファンコンを微調整した。
・Matrox M9120のドライバをUpdateした。
・パフォーマンス・消費電力とも殆ど変化なし。
やはりL3426+Matroxは良い。スクロールが滑らかで発色良し、Full-HD FlashもFull-HD TSも問題なし、Adobe CS3の動きも軽快だ。
|
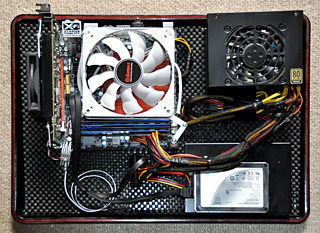 |
毎度お馴染みのお盆PC。
部品の交換が楽々、まな板に戻れないか。
|
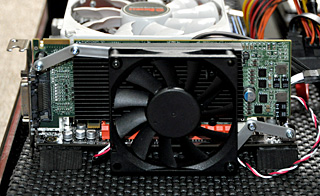 |
ファンレスのビデオカードMatrox M9120に80×15mmファンを載せた。
カードに空けられた使途不明の穴と
M/Bの穴を使って取り付けた。
|
|
あらいの錐 (2011.2.6)
|

PCケースをアルミ板で作るの場合、切断と穴開けの精度が問題となる。切断に関しては、糸鋸盤を使用し、サンドペーパーで仕上げれば、誤差1/4mm程度に収まるが、穴開けは一筋縄では行かない。 如何に正確な図面を起こしても、 ドリルの穂先が狙った位置からずれる事は珍しくない。抑もセンターポンチで正確なマーキングをすること自体が難しい。マーキングがずれれば、当然ボール盤作業も精度が失われる。アルミ板を接合する場合、ビスナット留めなら多少の誤差は吸収できるが、タップを立てる場合は修整が難しく、一発勝負で正確な穴開けが要求される。

あれこれ試行錯誤の末、穴開け位置のマーキングは、センターポンチではなく、「木工用の錐」で行うことにした。先が細いので正確なマーキングがし易い。ところが、安手の錐では直ぐに先が鈍り精度が保てない。やはり本職用の錐が欲しい。 あるある、その昔「あらいの錐」として日本一の評価を得たと言われる錐の刃が、我家に30本ほどある。近所の金物屋が廃業する時、整理品として入手したからだ。一流の鍛冶職人が一本一本鍛え上げた錐の刃と、HCで見かける廉価品とでは比較にならない。別次元の代物と言えよう。初めて使った時、切れ味・精度・耐久性とも、正に目から鱗が落ちる思いだった。そして、錐の刃は鉋や鑿と同じく研いで使うことを教えられた。
|
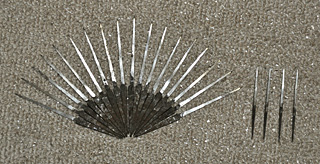 |
錐の名品「あらいの錐」
今となってはレア物、プレミアが付くかも。
|
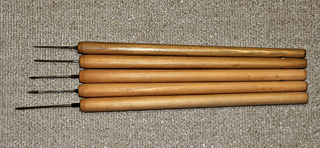 |
錐の柄は自分で作る。
今回は一番上の四ツ目錐を使う。
|
|
おっと、道具道楽の話を始めると切りがないので、錐の話はこれキリにしよう。
|
|

アルミ板を接合する時、ビスナットで留める方法は、簡単ではあるが手の入らない場所に適さない。アルミ板の一方にタップを使ってメスネジを切り出す方法は、そうした場所に好都合ながら、タップを切ること自体かなり難しい。

なぜ、タップ立ては難しいか。下の写真のような簡易タップ・ハンドルでは、刃の垂直保持に相当な熟練を要する。もし刃が傾けば、切り上がったメスネジはユルユルになり、十分な締付強度は得られない。 では、どうすれば良いか。 「ハンド タップ ガイド」なる便利な補助具も市販されているが、手持ちの工具で工夫できないものだろうか。
|
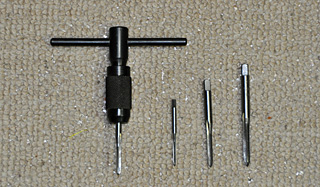 |
簡易タップセット
2/3/4/5mmの刃が付属する。
刃の垂直保持は難しい。
|
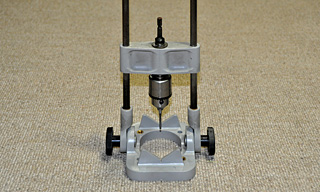 |
そこで、ドリル・スタンドに目をつけた。

タップの装着に問題はない。
ハンドルをどうするか。
|
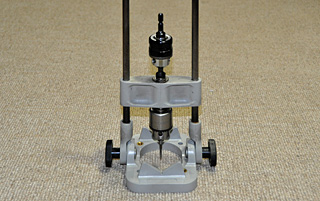 |
ドリルチャックを取り付けた。
多少回し易くなったが、二本のガイド棒が邪魔だ。
短く切り落とすか、もう一工夫するか。
|
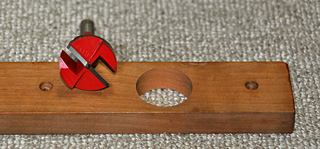 |
桜の端材で木製ハンドルを作ることにした。
丁度良い寸法のドリル刃がなかったので、
少し大きめの刃で穴を開けた。
|
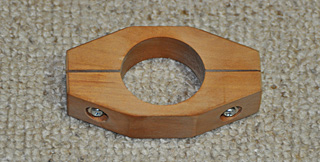 |
穴を開けた桜材を二つに割り、
ドリルスタンドに収まる長さに切断した。
|
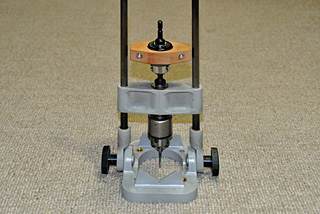 |
特製ハンドルをビスナットで固定した。
かなり良くなった。しばらく使ってみよう。

何れ、ガイド棒を切り落とすことになりそう。
|
|
試し切りをしたところ、ビスがしっかり留まるようになった。フリーハンドとは大違いだ。
何だか木工サイトの様相に・・・
|
|

出来上がったタップ立て治具をどう使うか。誤差1/4mm以下を目指すなら、そのままでは少々心許ない。
|
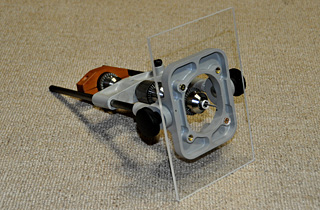 |
では先ず、タップ立て治具を安定させよう。 そのためには治具と素材との接触面を拡げればよい。話は簡単、ドリルスタンドに5mm厚の透明アクリル板を取り付けた。 (こ手法はトリマーでよく用いられる)

5mm厚のアクリル板を取り付けたら、タップ刃の出が不足気味になった。仕方ない、ドリルチャックをもう一段加えよう。ただし、回転軸方向に長さを増すと偏心の恐れがあるので、精度のよい製品を選ぶ必要がある。結局、家中のドリルチャックを総動員しても間に合わず、新たに1本購入することになった。ドリルチャックのトーテムポールだ。

タップハンドルを一定の力で滑らかに回転させるには、片手より両手の方が確かである。そうなると、素材と治具を固定しなくてはならない。

さて、「板金折り曲げ機」を使ってアルミ板を折り曲げた時、曲げ部分の外側は曲面になる。
これは好みにもよるが、接合部分を完全な直角に仕上げるなら、L型アングルを使う方法が最も簡単である。 (幅15mm、厚さ2mmのL型アングルを使う予定)

では、L型アングルを作業板にどう固定するか。
これも難しくはない。作業板に溝を掘ればよい。ただしその場合、L型アングルを載せた作業板と治具との接触面を水平に保つためには、二段の溝を掘る必要がある。
|
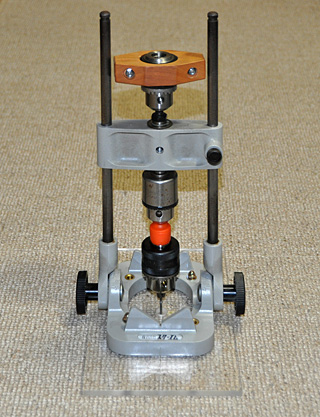 |
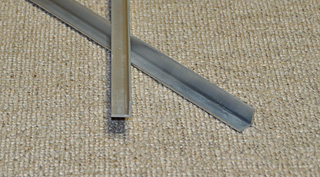 |
|
ケースづくりは道具づくりが決め手。 もう暫く、木工サイト風レポが続きそう・・・
|
|
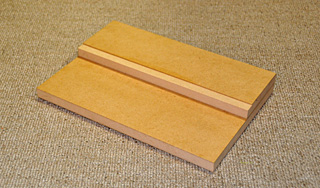 |
では、タップ立て治具用の作業板をつくろう。
材料は18mm厚のMDF(Medium Density Fiberboard)
この板は比較的平面性が良好なので、治具や作業板によく使われる。
|
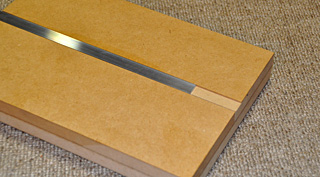 |
二段の溝を掘ると言っても、MDFを二枚重ねにすれば一掘りで済む。ルーターを使い幅13mm深さ2mm切り欠いた。 或いは2mm厚の板を追加すれば同じ結果が得られる。取り付けは、MDFの裏から木ネジで留める。
|
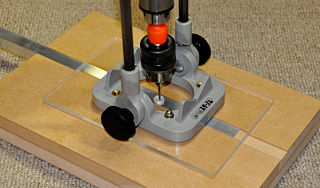 |
写真の作業板は、幅15mm厚さ2mmのL型アングル専用だが、必要に応じて幅と深さを決めればよい。
|
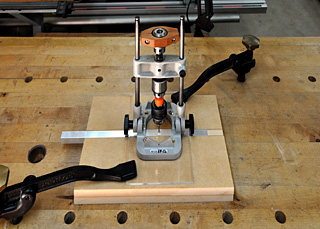 |
|
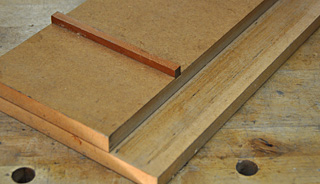 |
L型アングルの端を仕上げるには、左の治具を使う。これは木工用だが金工にも使える。
|
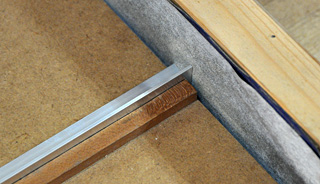 |
直角の確かな木片にサンドペーパーを貼り付けて擦る。
|
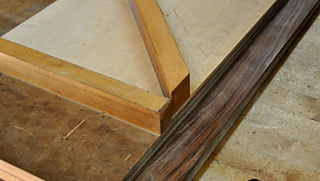 |
L型アングルの端を45度に仕上げる場合は、左の治具を使う。これも木工用。
|
|
|

本PCのケースを最初に計画したのは昨年の今頃だった。いきなりハイグレードな仕様を狙ったために中々実現せず一年経ってしまった。今回もまた、当初の計画通り進めるか、或いはグレードを落とした仕様に変更するか、そこが思案の為所だ。

何と言っても自作ケース1号機なので、未知の局面に出会うことは間違いない。木工の場合なら、穴を開け損じたら埋めることも、切り損じたら貼り合わせることもできる。アルミ材ではそうは行かない。部品の位置決めと穴開けにミスは許されない。特にリアパネルの作業は難しそうだ。やはり一歩退き、アルミ工作に慣れることを当面の目標にするべきであろう。

と言うことで、デザインを練り直すことにした。
・リアパネル以外一切のネジを見せない仕様は次回に送る。
・曲面仕上げも同じく見合わせる。
・デザインはシンプル、機能は必要最小限とする。
・吸気ファンは、フロント120x25mm 1個。
・排気ファンは、リア60x20mm 2個、両サイドに100x12mm 各1個。
・光ドライブはなし、電源はpicoPSU160。
・そして、工作ミスを見込んで6面を全てを独立し、差し替え可能にする。

各部の寸法は下表の通りである。 (単位:mm)
P55-T36 + L3426 + M9120 用ケース
|
横方向 (左から)
|
|
縦方向 (下から)
|
側板の厚み
|
2
|
底板の厚み
|
2
|
ファンガードの厚み
|
2
|
M/Bを固定するスペーサーの高さ
|
7
|
サイドファン
|
12
|
M/Bの基板及び上方のクリアランス
|
81
|
ファンとビデオカードの間隔
|
2
|
2.5"HDD消音ボックスの厚み
|
25
|
ビデオカードがM/Bからはみ出る分
|
6
|
HDD消音ボックスと天板の間隔
|
10
|
M/B
|
170
|
天板の厚み
|
3
|
M/Bとサイドファンの間隔
|
5
|
合 計
|
128
|
サイドファン
|
12
|
|
ファンガードの厚み
|
2
|
側板の厚み
|
2
|
合 計
|
215
|
|
奥行方向 (前から)
|
|
後板 縦方向 (下から)
|
フロントパネルの厚み
|
3
|
底板の厚み
|
2
|
フロントパネル2枚の間隔
|
12
|
M/Bを固定するスペーサーの高さ
|
7
|
フロント補助パネルの厚み
|
2
|
I/Oパネル
|
42
|
フロントファンの厚み
|
25
|
I/Oパネルとリアファンの間隔
|
7
|
フロントファンとM/Bの間隔
|
19
|
リアファン
|
60
|
M/B
|
170
|
リアファンと天板の間隔
|
7
|
M/Bとリアパネルの間隔
|
2
|
天板の厚み
|
3
|
リアパネルの厚み
|
2
|
合 計
|
128
|
合 計
|
235
|
|
|
ケースの寸法は、W215xH128xD235=6.47L
|
|

さあ、いよいよ製作開始だ・・・
|
|
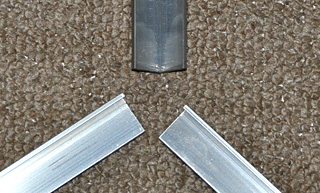 |
先ず、L型アングルの調製から始めよう。

L型アングルを三方向直角に固定する。
そのためには端を45度に仕上げ、適当な補助金具を使う方法が無難であろう。
|
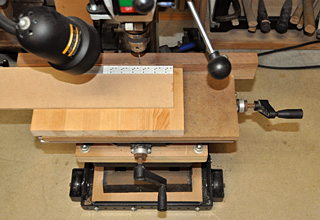 |
幅20mm厚2mmのアルミ板から補助金具をつくる。小さく切断してからでは、ビス穴を空けにくいので、事前に空ける。

ボール盤に WABECO社のX-Yテーブルを載せた。これで位置決めは完璧な筈なのだが。
|
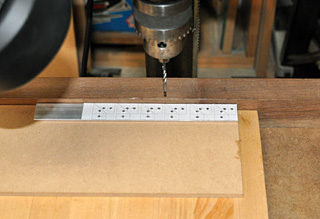 |
X-Yテーブルにフェンスを立て、Y軸方向調整ハンドルを使って前後の位置を固定する。
素材は下に敷いた棄て板と共に移動する。
左右の微調整はX軸方向調整ハンドルで行う。
(調整ハンドルには0.1mm刻みの目盛がついている)
|
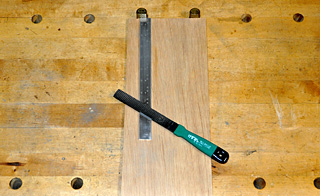 |
ボール盤で穴を空けた後、裏面のバリを取り除く。そのままでは糸鋸盤上でバタつく。

先ず、アルミ用のヤスリをかけた。
|
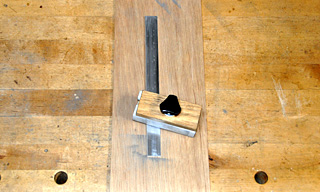 |
次にサンドペーパーで仕上げた。

サンドペーパ保持具は自作。
番手毎に幾つかあると便利。
|
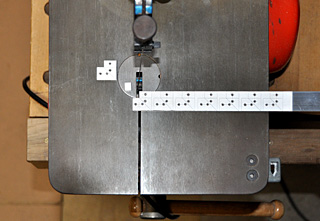 |
L型アングル固定用補助金具を切り出す。
2mm厚のアルミ板は糸鋸盤で簡単に切れる。
バンドソーの方がより速く切れるが、切断面の仕上げに要する時間を考えると、小物の場合、糸鋸盤の方が全体の作業時間は短い。
|
|

昨夜(2/11)は寒さが厳しく工房内は気温3℃、糸鋸盤のテーブルも同値。手がかじかんで作業は捗らなかった。暖房機を入れなくてはどうにもならない。
今日は家人用のオイルヒーターを借りよう・・・
|
|

木工房の暖房は気を使う。エアコンではフィルターが直ぐに目詰まりする。石油ストーブや電気ストーブでは、鉋屑が舞った時、燃え上がる危険性がある。そうなるとオイルヒーターあたりが無難か。他の暖房機に比べて決して強力とはいえないが、穏やかにじんわり暖まるので工房向きかもしれない。家人が旅行中の間だけだが。
|
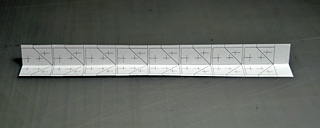 |
次に、もう一種のL型アングル固定用補助金具をつくろう。 これは同材のL型アングルを幅13mm長さ18mmに切れば事足りる。ビス穴は6ヵ所。
型紙は8個分。
|
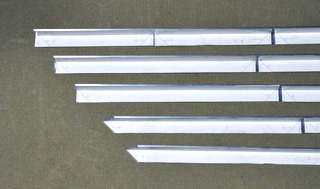 |
L型アングルに型紙一式を貼り付けた。

立体物のCADは面倒だ。
この型紙づくりにかなり手間取った。
骨組は45度に組み合わせるので、アングルの厚み2mmを考慮しなくてはならない。つまり、部分的に15mm厚のアルミ材を切断することになる。
|
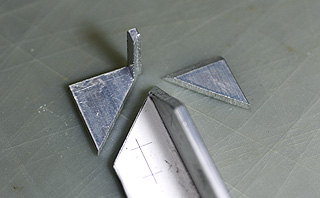 |
そのアルミ15mm厚部分を試し切りした。別段不都合はなかった。それにしても高々100Wのモーターで良く切れるものだ。 流石定評のある糸鋸盤だ。
|
|

以上で、L型アングル及び取付補助金具の仕様は決まった。
一応ここまでは構想通り運んでいる。明日は残りの切断と切り口の仕上げをしよう。
旨く収まるかどうか、それが問題だ・・・
|
|

骨組ができたので仮組した。
■う~ん、素人細工丸出しのようで気に入らない。
L型アングルを45度で接合するために大量のビスを使った。 角毎に10本、全体で80本である。いくら何でも多すぎる。ケースが出来上がれば見えない場所とは言え、余りにも知恵のなさ過ぎだ。

何故そうなったか。アルミ板を折り曲げれば、ビスの使用量は大幅に減るのだが、手持ちの板金折り曲げ機にアルミ材は1.5mm厚までとの制限がある。今回は2~3mmのアルミ板を用いる為、折り曲げ機は使えず補助金具が必要になったのだが、既製のL型アングル以外思い付かなかった。更に、兎角素人は必要以上の強度を求めがちとか。
■仮組に至るまでの間に幾つかのトラブルがあった。
・当初の予定では、ケースの高さは128mmだった。ところが、よくよく計算したら、120mmのフロントファンを取り付けるためには1mm足りないことが判った。結局、ファン防振ゴムの分も加えて4mm増し、132mmとした。
・型紙をアルミ板に貼り付ける際に使う「スプレー糊」がダメになった。中身はまだあるのに糊が出ないのだ。やむなく一般の糊で代用したが、アルミとの馴染みが悪く数カ所剥がれてしまった。当然、その部分の工作精度はガタ落ちになった。
・ビスの頭をアルミ板と面位置にするためには面取り用のドリル刃が必要になる。そこで、本ケースの為に刃を新調したところ、何時もの調子でドリルを回したら掘りすぎてしまった。作り直すにも材料切れ。取り敢えずワッシャを咬まして誤魔化すことにした。
・本ケースは、2.5mmビスの使用を予定していた。ビスの頭を小さくしたかったからだ。ところが、2.5mmのタップ刃が見付からない。 あるのは2.6mmばかり。2.5mmと2.6mmを混用すると先々面倒なので、2.6mmに統一することにしたものの、2.6mmビスの手持ちはなく、今日の仮組に間に合わなかった。
|
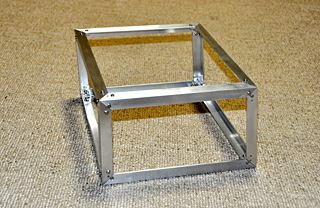 |
【骨組の仮組】

今一つパッとしない。ハッキリ言ってダサイ以外の何ものでもない。
|
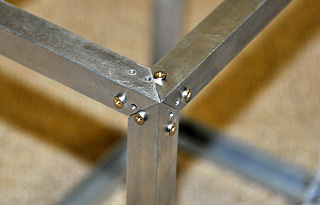 |
その原因はこれ。過ぎたるは何とかなり。

ネジは仮留め。実際にはビスの頭を面位置にするので、もう少し見てくれは良くなるかも・・・
|
|
|

2.6mmビスを入手し、骨組を本組立した。ところが、またまた不都合があった。2.6mmビスは2.5mmビスより頭の径が0.2mm大きい。 そのため一部の個所でビス同志がぶつかり、骨組全体の精度に無視できない影響が出た。結局、2.5mmビスに戻した。

再組立の後、しげしげと眺めた。何事も見慣れれば気にならなくなるようだ。一日経ったら「メカニックでいいジャン」に。
|
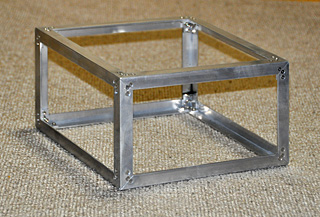 |
では、精度は如何に。誤差1/4mm以下の目標は達成されたであろうか。残念ながら○ではない。1/3mmほどの誤差がある。やはり型紙が剥がれたせいか、貼り直しても元通りにはならなかったようだ。だからと言って作り直すには忍びない。パネルを据える時に薄いワッシャを咬ませることで手を打とう。
(木工なら鉋をかければ済むのだが)

L型アングル三方向直角接合は、まあまあの仕上りだった。木工用の45度治具がアルミ材にも十分役立つことが判った。もし、その治具がなければ、今回の計画は難しかったであろう。
|
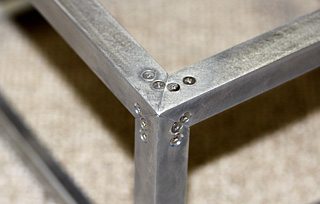 |
|

以上の骨組は、全てビスナットで留めた。そうなると、ナットが緩んだ時のトラブルが心配される。ファンやHDDなどの回転系部品から生ずる振動により、時間の経過と共に緩みがちになる。そこで、「ネジロック」なる緩み留め剤を使用することにした。

次回は、底板と後板をつくることにしよう・・・
|
|

底板と後板の図面を起こし始めたが、どうもスッキリしない。なぜなら、部品の寸法を測ること自体相当難しいからだ。インチ規格の部品をミリ単位で採寸すると極めて半端な数値になり、読取りに迷う。

例えば、後板に嵌め込むI/Oパネルを測ると
縦 44.??mm 横 158.??mm
??の部分は測る度に異なるので、44.5と159.0で妥協することになるかも知れない。

ところがインチ物指しで測ると
縦 1-3/4inch、横 6-1/4inch
とキッチリ測れる。

Mini-ITX M/Bは、
普通の物指しで測ると・・縦横 170.??mm
インチ物指しで測ると・・縦横 6-11/16inch

そうなると、PCケースは始めからインチ単位で図面を起こした方が良いのだろうか。これもまた難しい問題だ。と言うのも、アルミやアクリルなどの素材はミリ単位なので、図面を起こす時にミリからインチへ換算しなくてはならない。結局、何れにしても換算は免れない。幸い手元にインチとセンチ兼用の物指しとノギスがあるので、インチ物指しで採寸した後、Excelを使ってミリ換算することにした。
(インチ定規は法律によって販売が禁止されているそうだが、PC自作erなら1本は欲しい。探せばある)

|
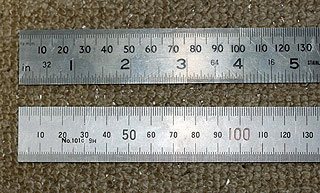 |
【計量法違反物いろいろ】

上は センチ・インチ兼用定規
下は 一般的なステンレス定規
|
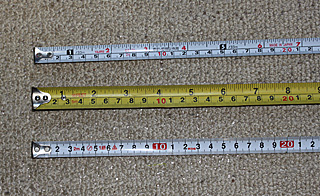 |
上は センチ・尺寸兼用巻尺
中は センチ・インチ兼用巻尺
下は 一般的な巻尺
|
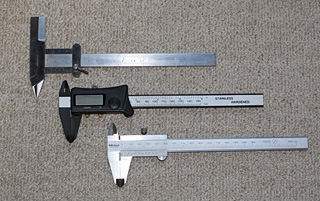 |
上は センチ・尺寸兼用ノギス
中は センチ・インチ兼用ノギス
下は 一般的なノギス
|
|
|

インチ規格部品の採寸に手を焼きながらも、どうにかリアパネルを仕上げた。
I/Oパネルも拡張スロットも一発で決まった。
|
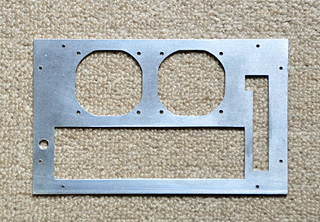 |
2mm厚のアルミ板は 大幅に切り抜いても確りしている。誤差は極僅か。
|
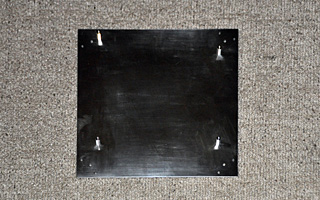 |
底板の製作は比較的簡単。
M/B取付穴の位置に気を付けるだけ。
(撮り方によって質感が全く違う 上はストロボなし、左はあり)
|
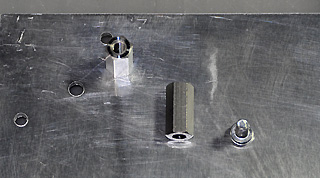 |
M/B取付スペーサーは、底板にタップを切らず、
裏からビス留めした。
|
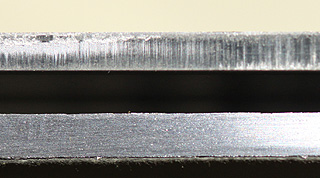 |
左の写真中、上は購入時のアルミ切断面。
下は糸鋸盤で切断した後、サンドペーパーで仕上げた時の切断面。(塗装をかける面は、もう少し荒目にする予定)
|
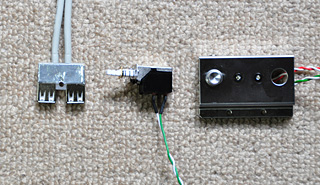 |
次は、前板の補助板をつくろう。
そのためには、電源スイッチとUSB端子の取付方法を考えなくてはならない。(リセットスイッチはなし)
|
|
|

フロントに取り付ける120mmファンを隠すために、フロントパネルを二重構造にした。
今日は、その内側のパネルを作った。
|
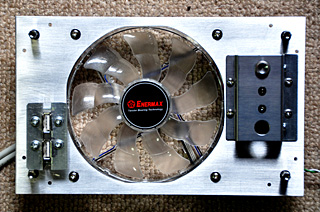 |
その補助板にPower SWとUSB端子を取り付けた。SWはAbeeのオプションパーツを、USB端子はMSIの古いM/Bに付属する拡張スロット用ブラケットから流用した。

左上の写真中、四隅のスペーサーにフロントパネルを取り付ける予定。

フロントパネル二枚の間隔は、SWボックスの都合により、当初の予定より3mm増して15mmになった。
SW本体は AINEX PA-062。感触は少し硬め。
|
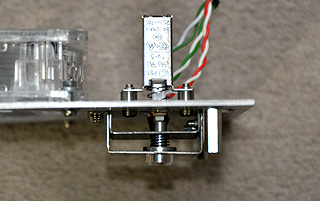 |
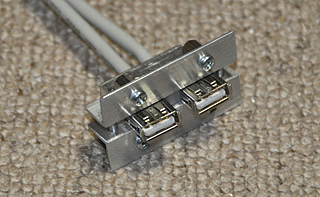 |
補助板の製作で最も面倒だったのはUSB端子である。なかなか思うように決まらず、取付金具を三度作り直した。
|
|

漸くPCケースらしくなってきた。ここまでで全体の1/3くらいか。まだまだ先は長い。
|
|

HDDとSSDの取付方法を考えよう。本機のドライブは SSD×1、HDD×1。
|
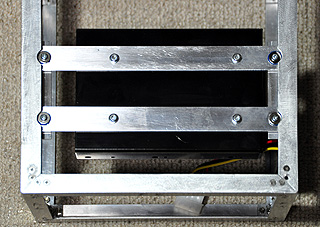 |
消音ボックス入り2.5"HDDは 3.5"HDDと同寸。
天板下に桟を渡し、吊すように取り付けた。
このケースにHDDは1台だけ。フロントファンを92mmにすれば2台積める。
天板とHDDの透間は8mm。
|
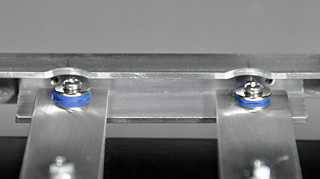 |
HDD取付桟はフレームに小さな棚を作って載せた。ここは手が入りにくいので棚板にタップを切った。2mm厚なのでビスの締まりは良い。
念のためにゴムブッシュを使って留めた。
メンテ時は桟橋ごと取り外す。
|
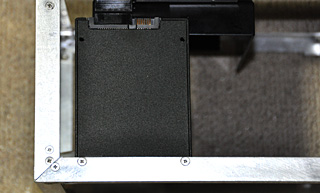 |
SSDはフレームに直付けした。2点留めだが大丈夫であろう。SATA及び電源ケーブルは、L型タイプでないと収まらない。
|
|

i3 2100Tが明日届くことになった。 早速H67CFで試したいところではあるが、本ケースが出来上がるまでは我慢しよう。それにしてもケースづくりは時間がかかる。何時になったら目途が立つのか見当もつかない。毎日少しずつ前進はしているのだが・・・
|
|

ここまで使用したアルミ板は全て2mm厚である。切断工具は糸鋸盤、仕上げはサンドペーパーである。今回は6.5L程度の小型ケースなので、1.5mmで十分と思われたが、タップを立てた時、板が薄いと締付強度に不安が残るため厚手の材料を選んだ。今のところ、この選択は正解と思われる。タップ立て治具のお蔭もあり、ビスは確り留まる。

さて、糸鋸盤による切断の精度には相当なムラがある。糸鋸刃の取付精度、刃の張力、刃の劣化、往復運動回数、作業場の明るさ、そして集中力を含めた体調など、精度に関係する要因は幾つもある。中でも刃の張力と往復運動回数は、素材によって最適値が異なるため、何度も試し切りをした後、糸鋸盤をセットしているが、それでも思うようには切れない。では、実際の切断面を見てみよう。
|
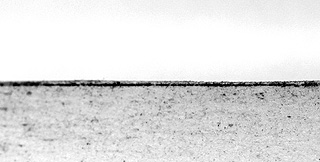 |
左の黒い筋が型紙の極細線。
|
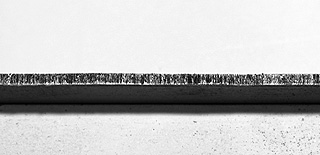 |
もう少し精度が良い時もそうでない時もある。
切断誤差は1/5~1/3mmくらいか。
|
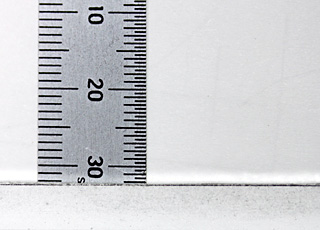 |
この程度の誤差なら、サンドペーパーを貼った鏡の上で擦れば十分真っ直ぐになる。 入り組んだ場所なら、木片にサンドペーパーを貼って擦ればOK。

何時もこのように切れれば良いのだが・・・
|
|

これまでに糸鋸の刃は8本使用した。その内半分は切れ味が落ちたため、残りの半分は作業中に切れたためである。刃が切れる理由は幾つかある。 (刃は1本 64円)
・アルミ材の送り速度を上げ過ぎて、刃に無理がかかった時。
・素材を糸鋸盤に押しつける力が不安定な時。
・素材の送り方向がブレた時。
・素材の裏にバリが残っていると糸鋸盤上でバタつくが、少しだからと気を緩めた時。
総じて、素材が小さい時ほどブレ易く、刃も切れ易い傾向にあるようだ。
|
リアパネルに部品を取り付けた (2011.2.23)
|

後板に部品を取り付けよう。その為にはフレームの一部を切り欠かなくてはならない。
2個の60mmファン及びI/Oパネルに当たらぬよう、幅を調節した。
|
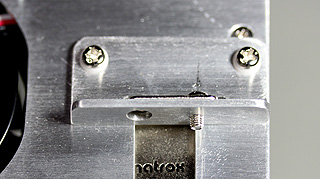 |
拡張カード固定金具は、10×20mmのL型アングルを利用し、最も簡単な方法を選んだ。
|
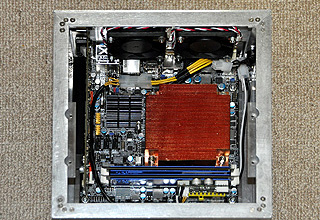 |
メモリのヒートスプレッダを薄手の物に替え、picoPSU160を直差しした。
6面開放構造なので部品の取り付けは楽々。
|
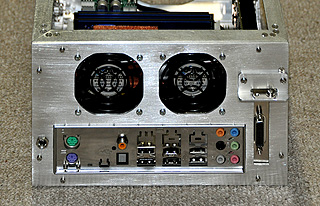 |
どうにか収まった。
ACアダプタ電源のコネクタもギリギリ入った。
リアパネルは「クリアラッカー焼付塗装」をする予定である。焼付と言っても至極簡単。カラースプレーを塗布した後、生乾きの内にガスレンジの上で炙ればよい。アルミ板に空けられたビス穴に針金を通して吊せば火傷はしない。その昔、この手法はオーディオアンプの製作時によく用いたが、30年以上経ても剥離はない。
|
|

ケースづくりで最も辛いことは何か。CADでもアルミの切断でもない。「スプレー糊剥がし剤」の臭いである。特別「化学物質過敏症」ではないのだが、その臭いを嗅ぐと、即頭痛になる。マスクと手袋を着け屋外で使用しても防ぎきれない。 かと言って、他に良い方法を知らない。
|
フロント補助板に部品を取り付けた (2011.2.24)
|

ケースの高さを当初の予定より4mm増したため、120mm+ファン防振ゴムは楽々入った。
|
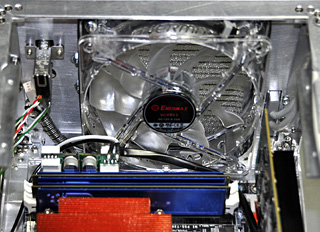 |
電源SWやUSB端子が他の部品と干渉しないことを確認した。
|
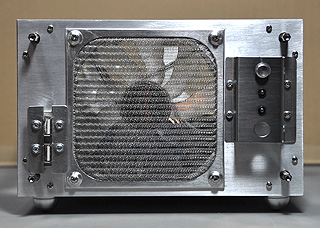 |
120mmファンは安心感がある。
ファンフィルターは再検討するかも知れない。
インシュレーターはAbeeのオプション部品。

フロント化粧パネルを取り付けたらどうなるか、
それが心配だ。
← 写真をクリックすると拡大します。
|
|

次回は側板をつくる予定だが、サイドファンは左側1個で良いように思えてきた。側板の加工は何時でもできる。右側板の穴開けは先送りにしよう。
|
|

サイドパネルの厚みをどうするか、まだ思案中である。2mm厚で十分なのだが、問題は使用するビスの数だ。3mm厚なら4点留めで良いのだが、サイドパネルに100mmファンの穴を空けるため、2mm厚ではビスの数を増やす必要があるかも知れない。2mm厚のフロント補助板に120mmファンの穴が空けたら歪み易くなった。サイドパネルの厚みを決めなくてはフロントパネルも決まらない。もう一つ絡みがある。サイドパネルの厚みによってフロントパネルを取り付けるビスの位置に影響がでる。そこで少し厚手のコピー用紙を使って型紙をつくり、実際に取り付けてみた。
|
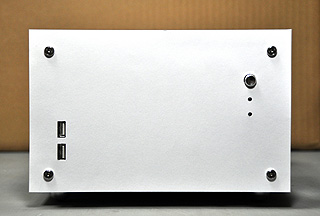 |
四隅のビスが少し内側に寄っている。サイドパネルの厚みを増すと更に内寄りになる。ビスの位置を替えるにはフロント補助板を修整しなくてはならない。
|
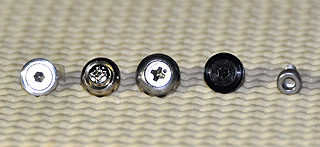 |
四隅に使うビスを色々試した。どれにするか決めかねている。上の写真では下の写真中左端のロゼットワッシャー+ヘクサロビュラねじを使った。
|
|

それにしても味も素っ気もない顔だ。もう一工夫するか、アルミの質感だけで見せるか・・・
|
|

サイドパネルとフロントパネルを同時につくった。
後者は3mm厚のアルミ板。切断に要する時間は2mm厚の倍くらいかかった。
|
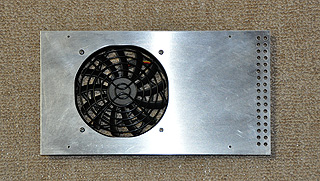 |
左側板に100mmファンを取り付けた。 右側板にはファン穴はない。 側板と天板は黒の艶消し塗装をかける予定。 右端の穴はフロントファン吸入口。
径4mm×34個。ドリルの刃を2.2/3.2/4.0mmと3回替えて空けた。
|
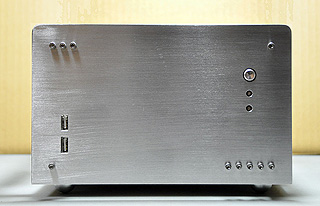 |
四隅のネジは 3mmの六角穴付ボルトを選んだ。
余りにもノッペリしているので飾りネジを配した。
上両端の円味は丸鉋の曲面を利用して仕上げた。
アルミヘアラインは仮仕上げ。
レタリングするか思案中。
← 写真をクリックすると拡大します。
|
|

アルミ板の切断作業は天板を残すだけになった。 あと一息だ。
|
アルマイト加工 (2011.3.2)
|

アルミ板の端切れを使って黒の艶消し塗装を試みた。結果は×。乗りが悪く手の脂も目立ち易い。素人塗装では台無しだ。一奮発してアルマイト加工に出そう。

そこで、Web上から市内の業者を探し見積りを取った。安くはないが法外でもない。
迅速かつ丁寧な業者に当たったようで、メールのやり取りを三往復した結果、業者に出すことにした。天板を仕上げたら発注する予定である。
|
道草 (2011.3.2)
|
■ 時には息抜きも必要だ。一つの事ばかり夢中になっていると、とかく視野が狭くなり新しいアイディアが浮かびにくくなる。と小理屈をつけて ASRock E350M1/USB3 を試した。
【M/B】ASRock E350M1/USB3
【CPU】AMD E-350 Dual-Core (M/B付属)
【MEM】DDR3-1333 2GBx2
【SSD】Transcend TS128GSSD25S-M
【PSU】picoPSU160
【Case】お盆
【OS】Win7HP64sp1

Win7HP64のインストールは無事に終わったが、Updateはスムーズでなかった。フリーズと勘違いするほど遅い場面もあり、待ちきれずに危うくリセットをかけるところだった。それでも我慢をしてsp1まで到達した。OSのインストールだけではなく、圧縮ファイルの解凍やアプリケーションのインストールも苛つく。気の短い人には向かないかも知れない。ところが、実際にアプリケーションを起動すると遅いなりにも底々動くので、ダメ出しするまでには至らない。

【Win7 Score】 3.8 5.2 4.4 5.7 5.9
【Superπ104万桁】 49秒
【Yume1024×768最高】 10159
【3DMark06】 10分待ってもスタートしない
【アイドル時消費電力】 18W
【Prime95実行時消費電力】 33W
【高負荷時消費電力】 38W (Windows Experience Index実行時ピーク値)
【BDの再生】 良好 (PowerDVD9Ultra)
【Full-HD TSファイルの再生】 ファイルをローカルドライブに置けば良好
【HD Flashの再生】 1080pは×、720pまでか
■ 2Core 1.6GHzのCPUとしては、まあまあの成績か。 中でも高負荷時消費電力38Wは好ましい。60W程度のACアダプタでも行けそうだ。では、動作がトロいこと以外に問題点はあるだろうか。

それがあるのだ。スリープから復帰せず、放っておくとハングし再起動するのだ。 時には無事に復帰することもあるので原因の特定が難しく、メモリを替えたりBIOSを弄ったりしてはみたものの、今のところ問題の解決には至らない。

また、CPUファンが静かとは言えない。そこで付属の40mmファンを50mmファンに差し替え、BIOSのファンコンで約3000rpmに設定したら十分静かになった。更に120×10mmファンを800rpm程度で回し、M/B全体に風を当てた。 これなら小型のケースに入れても心配ないであろう。

現状ではこのE350M1/USB3を常用PCに仕立てるのは厳しい。スリープ復帰の件以外にも再起動に失敗するとか、ご機嫌麗しからざる場面がある。M/Bに問題があるのか、自分の使い方が悪いのか、判断が難しい。何れにしてもBIOSの更新を待つことにしよう。
|
|

天板はビス穴4個所だけの簡単な仕様である。直ぐにも作れるのだが、中々手を出せない理由がある。アルミ板の端をどう仕上げるか決まっていないからだ。箱の角を仕上げる場合、30/45/60度の角張った面取りをするか、坊主面と称する曲面仕上げにするか、暫し悩まなくてはならない。仮に坊主面を選んだ場合、曲率をどの程度にするか。更には、その曲面の基準となる治具をどうするか。

簡単かつイージーに済ませるなら、サンドペーパーで何となく円味を付ければ事足りるが、木工愛好家の端くれとしては受け入れ難い。明確な意志を持って角を決めたいのだ。
よし、3mm厚のアルミ板を坊主面に仕上げよう。
|
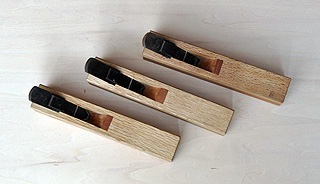 |
手元に木工用の坊主面鉋が三丁ある。
半径1分/1分5里/2分、即ち、半径3.0/4.5/6.0mmの曲面仕上用鉋である。今回使用する天板は3mm厚なので、半径3mmの曲面仕上げは可能である。だが、その鉋でアルミを削る訳には行かない。
フロントパネルの角を丸く仕上げた時は、2分の坊主面鉋にサンドペーパーを当てて使ったが、これはほんの僅かな部分だったからであり、長さ230mm程ある天板の仕上げにゴシゴシ使えば、坊主面鉋の台を痛めてしまう。
|
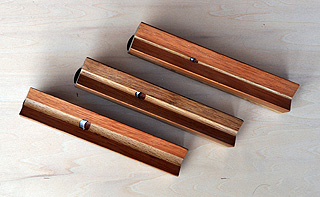 |
|

とするなら、
・アルミ板を坊主面に仕上げる治具をつくらなくてはならない。
・その為には直径6mmの溝を掘る必要がある。
・6mmの溝はルーターで掘れる。
・ルータービットは明日届く予定である。

道草のお蔭かも知れない。 少し面白くなってきたぞ・・・
|
|

直径6mmの溝を掘るルータービットを入手した。早速着手したいところではあるが、そうは行かない。 アルミ板を坊主面に仕上げる治具は木工作業が主体になる。 そのためには工房を掃除しなくてはならない。アルミの切り屑と研磨した微塵が充満している中で鉋がけ作業はできない。そこで、金工道具を一旦片付けて本来の木工房にすべく大掃除をした。久し振りに片付いたので写真を撮った。 この際だ、全部見せてしまおう。
|
|
U溝ルータービット
これ1本で廉価ケースが買える
|
|
工房の鉋コーナー
中段から上は小鉋及び特殊鉋
大部分は新潟の鉋鍛冶師から直接購入した
右手はドリルビット&ルータービット類
|
|
玄翁・木槌・ドライバー
右手にペンチ・プライヤーなど
|
|
スケール・ノギス・スコヤ類
下段はサンドペーパー保持具
|
|
鑿コーナー
凡そ1/3は市販品、1/3は特注品、
残りの1/3は古道具屋から購入
左手前はボール盤
|
|
クランプ類
ホースは集塵機用
上段はホースのジョイント類
|
|
砥石コーナー
凡そ2/3は天然砥石、1/6は合成砥石、
1/6はダイアモンド砥石
砥石棚の上は自動かんな盤置場
|
|
手前がテーブルソー、その奥がバンドソー
左手にネジ棚、中央奥に各種鋸
工房内の棚は全て自作

ガラス戸の向こうは物置、ここは元車庫
|
|

その他写真に写らなかった工具
【手工具】 鉈・鉞・手斧・槍鉋・各種小刀・毛引・白引・セン・バンカキ・彫刻刀など
【電動工具】 ルーター・トリマー・ドリルドライバー・ジグソー・サンダー・自動かんな盤・
手押しかんな盤・フライス盤・旋盤・グラインダー・集塵機・コンプレッサーなど・・・

一体全体こんなに道具を集めてどうするのか。本ページをご覧の多くの方はそう思われることでしょう。 正にクレー爺・・・
|
|

入手したU溝ルータービットを使い、タモ材の角を半径3mm切り欠いた。
そのままではサンドペーパーが落ち着かないので別の角材で挟むことにした。研磨面は3mm幅で磨くためサンドペーパーは直ぐにすり減る。 そこで、アルミ板との接触面を少しずつずらせるように蝶ナットを使って固定することにした。

では、2mm厚のアルミ板の端切れを使ってテストしてみよう。
テストとはいえ、いきなり本治具を使って加工する訳には行かないので、
・先ず、中目の平ヤスリで大凡の形をつくる。
・目の細かいヤスリに替えて形を整える。
・平らなサンドペーパー保治具を使ってムラを取り除く。

いよいよ坊主面治具の出番だ。
・治具に#150のサンドペーパーを取り付けて擦る。
この時、アルミ板を垂直に立てて作業台に固定した。
・サンドペーパーを#220・#280・#320・#400と順次番手を上げて仕上げた。
厚手のサンドペーパーでは半径3mmの曲面が縮まるので、#150あたりから始める
のがよさそうだ。
|
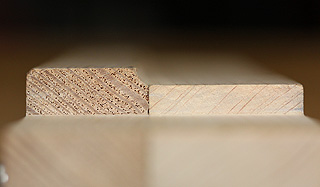 |
ルーターで切り欠いた半径3mmの円弧。
左はタモ材、右はヒノキ材。
|
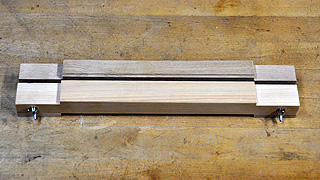 |
蝶ナットを使ってサンドペーパーを固定する。
簡単な仕組だが、考案するのに丸一日かかった。(全長340mm)
|
 |
#150より目が細かければ、サンドペーパー自体が薄くなるので、円弧に馴染み易い。
|
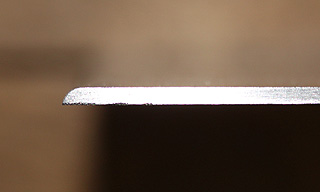 |
2mm厚のアルミ板に半径3mmの坊主面処理をしたため、中途半端な円弧になった。3mm厚のアルミ板ならもう少しマシになるだろうか・・・
|
|
|
■ いよいよ天板をつくる段になった。その前に接合部分を念入りに調整し、誤差を最小限に押さえ込もう。ヤスリとサンドペーパーを使って丸一日悪戦苦闘の結果、どうにか1/4mm程度の誤差に収まった。

ところが、天板に予定している300x420mmのアルミ板を当てたら直角が合わない。調整の際、信頼できるスコヤを使って確認した筈なのにどうしたことか。 原因は直ぐに判った。
購入したアルミ板が長方形ではなかったのだ。 3mm厚のアルミ板は切断に時間がかかるので、できれば元のアルミ板の二辺をそのまま使いたいのだが、今回はダメ。三辺仕上げなくてはならなくなった。
■ 同じような経験は15年程前にもあった。本格的に木工を始めた頃、出来上がった作品の精度が思わしくなく、何事も一筋縄では行かないものと、自らの未熟さを歎いて許りいた。ところが、ある時ふと 「スコヤは必ずしも直角ではない」 ことが判った。廉価品は誤差の許容範囲が広いからだろうか、これでは精度が上がらない訳だ。そこで信頼できるスコヤを求めたら雲泥の差、作品の精度は一気に向上した。今回のアルミ板も然り。規格品だから正確とは限らない。市販の素材は、大体真っ直ぐ、大凡直角と心得るべし。
■ 能書きはこれくらいにして作業を始めよう。先ず、直角を決めた。長さ300mmに対して1mm近い誤差があった。 ひたすらヤスリがけとサンドペーパー仕上げ。 修整に小一時間かかった。その後、糸鋸盤で必要な寸法に切断し、サンドペーパーで仕上げた。例の坊主面処理は思いの外簡単だった。ヤスリがけ、平サンドペーパー、そして坊主面治具による仕上げ。30分程で仕上がった。

次に、取り付けビスの穴を空け、フレームにタップを切った。ネジの頭が面位置になるよう面取りをした。裏面は電動サンダーをかけ、表はヘアライン加工をして、アルマイト加工に出す前処理は終わった。再度組み立てて写真を撮りたいところではあるが、傷を付けたくないので今日のレポは写真無し。 加工業者は車で30分くらいの所なので、明日持ち込むことにした。
|
|

■ アルマイト加工は1日で仕上り、今日の午後4時に受け取ることになった。何と言っても初めての自作PCケースなので少しドキドキする。2号機はあるか、1号機で終わりになるか、出来映え次第になりそうだ。

2/6に着手してから丸一月、 ケースづくりに掛かりきりだった。 寝ても覚めても頭の中は図面でいっぱい、夜中に新しいアイディアが思い浮かべばガバと起き上がってCADをする日々が続いた。そうしたワクワク感は悪くない。とは言っても感傷に浸るほど若くはない。頭を冷やして反省しよう。

では、所要時間はどの位か。正確な時間は判らないが、構想とCADに要した時間を含めて凡そ100時間、実際の工作時間はその半分の50時間程。 掛かった費用を概算すると、アルミ板・L型アングル・ビスナット類を合わせて12,000円程度か。その中にアルマイト加工費は含まれていない。勿論、手間賃もタダ計算だ。 仮に、このケースの値段を20,000円とすると工賃は8,000円、時給に換算すると8,000円÷50時間=160円。一月遊ばせて貰ったことを考えれば御の字と言えようか。
■ もし2号機をつくるとしたら、何はともあれ工作時間を短縮したい。そのためには便利な工具を導入する他はないであろう。 今回、最も時間の掛かった行程は、アルミ板の直線仕上げとアングルの45度仕上げ、つまり、サンドペーパーでゴシゴシ、時にはヤスリでゴリゴリ擦る作業だった。そうした作業を合理化する電動工具と言えば、ドイツ ヘグナー社の「ディスクサンダー HSM300」がある。現在、同社の製品は円高差益還元セール中で購入のチャンスではあるが、それでも安くはない。

更に、ボール盤による穴開けの精度を向上させるためにもう一工夫したい。上に述べた「あらいの錐」を使ってもドリルの穂先は狙いを外すことがある。あれこれ調べたら強力な助っ人が見付かった。レーザー光線を利用したドリル刃の中心ガイド装置である。同系統の製品に、角度や高さやをデジタル表示するアイテムもある。 何れも手頃な価格なので、そう悩まなくとも購入に踏み切れそうだ。

頭を冷やして反省どころか、新たな散財になりそうな話ばかりではないか。 と言うことは、既に関心は2号機に向いていることになるのだが・・・
|
|

アルマイト加工済みのパネルを取り付けた。自作1号機としてはまあまあの出来か。
(細部の写真は、後日部品を取り付けてからアップします)
|
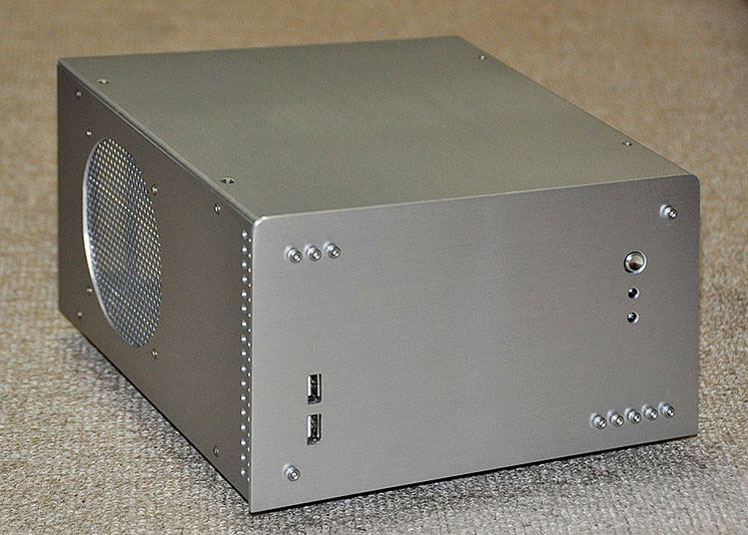 |
|

完成写真をUPしてから本サイトのアクセス数は倍増し、一晩で2000を越えました。どうにか格好がついてホっとしています。製作中に多くの方から激励の言葉を戴きありがとうございました。反省点が少なくありませんので2号機をつくることになりそうです。

また、自作ケースばかりか工房の写真も注目されているようです。どうしてそんなに道具を集めたのか、G3は職人か等々。いいえ、職人ではありません。10数年前から年に1・2回「日本の伝統技法」について講話をする機会があり、理屈だけではなく実際に検証するため道具を揃え始めました。 その一部は本業にも役立っていますが、8割方は道楽です。
では、本業は何か。 サイト上では「?」のママにしておきたいと思います。 但し、メールを戴いた方には明かしていますので、関心のある方はご一報下さい。

2号機の構想は、Mini-ITX M/B・ビデオカード・サウンドカード・PT2・SSD・スマドラ入り3TB HDD・BDドライブを収める小型ケースです。1号機を仕上げた後、桜の花の咲く頃に着手できればと思っています。

昨夜、 ヘグナー社のディスクサンダー HSM300 が届きました。もう後戻りはできない・・・
|
|
3/9に出来上がった自作PCケースに部品を収め始めましたが、3/11の大地震以来、組立途中のママになっています。
|

日本史上最大の地震と津波により東北地方太平洋岸の地域では甚大な被害に見まわれました。刻々と被害状況が明らかになるにつれ、想像を絶する惨状に言葉もありません。一人でも多くの方が無事であられることを祈るばかりです。

我家には宮城県出身の職員がいます。 彼の実家はやや内陸部の古川にあり、津波の被害は免れたそうですが、それでも新築したばかりの家は大きな被害を受けたそうです。祖父母の住む気仙沼の本家や親類とは未だ連絡が取れないそうです。

当地横浜の被害は比較的小さく、 外壁が崩れたり舗道のタイルが波打ったりした程度に留まりました。中でも筆者が住む保土ヶ谷は揺れも少なく被害は殆どありませんでした。

地震発生時、かなり大きな揺れで始まりました。直下型の地震とは異なり、振幅は大きいものの周期の長い揺れで、家具や建具が騒ぐこともありませんでした。ところが、1分以上過ぎても止むことがないので屋外に出て周囲を見渡したところ、近くに立つ100m超の高層ビルが波間の船の様に大きく揺れ、今にも窓ガラスが飛び散るかと心配されました。丁度下校途中だった小学生10数人を広場に誘導し暫く様子をみました。恐怖に戦き泣きべそをかく児童もいましたが、やがて揺れは治まりそそくさと帰って行きました。それから30分後、二回目の大きな揺れが襲いました。 一回目よりは多少弱く、2~3分で終息しました。家の内外を確認したところ、工房内に縦置きしてあった充電式ドライバが倒れたこと以外に変化はありませんでした。そうこうする内に、職員の新妻がやってきました。箪笥や戸棚の抽斗が飛び出し、一人では怖くていられないとのこと。と言うことは、同じ保土ヶ谷でも所によって大きな違いがあることになります。

我家のある場所は、古代は波打際、中世に陸化したと考えられる標高5mの地で、地面を1mも掘れば岩盤が現れる極めて地盤の安定した所です。やってきた新妻が住むマンションのある場所は、江戸時代の始めに小河川の岸辺から宿場の町並に整備された標高3mの地。つまり、地盤によって揺れに大きな違いがあることになります。こうした時こそ、郷土史の記述は心強い味方になることを改めて思い知らされました。或る宗教団体の信者の話によれば、我家のある一帯は横浜市内でも最も地盤の安定した地域で、激甚災害時の避難場所として密かに指定しているとも聞き及んでいます。確かに、隣の山には湧水があり、雑木を切り出せば当分の燃料になります。工房には薪をつくる鉈や鉞は勿論、製材用の大鋸もあり、仮に全てのライフラインが止まっても一週間くらいは生き延びられそうですが、そう言う日がやって来ないことを祈る許りです。
|
PCを組み立てる代わりに古典を紐解きました。
|

この度の大地震の規模は日本史上最大のM9.0とのことですが、これまでの記録は平安時代の貞観十一年 (西暦869年)5月26日 (陽暦では7月13日)の陸奥国大地震 (M8.0~8.6)と言われています。そこで、その記述を「日本三代實録 巻16」から引用します。

(原文)
五月廿六日癸未。陸奧國地大震動。流光如晝隱映。頃之。人民叫呼。伏不能起。或屋仆壓死。或地裂埋殪。馬牛駭奔。或相昇踏。城郭倉庫。門櫓墻壁。頽落顛覆。不知其數。海口哮吼。聲似雷霆。驚涛涌潮。泝洄漲長。忽至城下。去海數十百里。浩々不弁其涯。原野道路。惣爲滄溟。乘船不遑。登山難及。溺死者千許。資産苗稼。殆無孑遺焉。

(訳文1 漢和辞典・古語辞典のみによる)
五月二六日癸未 (陽暦7月13日)陸奥国の地が大きく揺れ動いた。波間に揺れる月の光は昼間の様な陰を映した。この頃、人々は泣き叫び、身を伏せた者は起き上がることができず、或る者は倒れた家屋の下敷になって圧死し、或る者は裂けた大地に飲み込まれた。馬や牛は驚き走り、或いは互いに絡み合った。城郭、倉庫、門、櫓、墻壁などは崩れ落ちて転覆した。その数は計り知れない。

海の口では大きな唸りを上げ、その声は雷鳴のようだった。逆巻く大波が涌き上がり、溢れかえって遡った。忽ち城下に至った。海から凡そ10Kmはあろうか。広々として涯を判別することもできない。原野も道も惣て大海原と化した。船に乗る間もなく、山に登ることもできず、溺死者は千人ほどあった。家財・稲苗など、残る物は殆どなかった。

(訳文2 他の訳文も参考にした)
五月二六日癸未 (陽暦7月13日)陸奥国の地が大きく揺れ動いた。発光現象が見られ昼間の様な陰を映した。この頃、人々は呼び叫び、寝ていた者は起き上がることができず、或る者は倒れた家屋の下敷になって圧死し、或る者は裂けた大地に飲み込まれた。馬や牛は驚き走り、或いは互いに絡み合った。城郭、倉庫、門、櫓、墻壁などは崩れ落ちて転覆した。その数は計り知れない。

海嘯 (=津波)は大きな唸りを上げ、その音は雷鳴のようだった。逆巻く大波が涌き上がり、溢れかえって遡った。忽ち城下に至った。海から5~7Kmはあろうか。広々として涯を判別することもできない。原野も道も惣て大海原と化した。船に乗る間もなく、山に登ることもできず、溺死者は千人ほどあった。家財や稲苗など、残る物は殆どなかった。 (訳:PCG3)
-----------------------------------
同じ文章が「陸奥国地大震、海嘯、溺死千許」として「日本災異志」に採録されています。古くは、津波と海嘯 (かいしょう)が同義に使われていたように思われます。
(拙い訳文で申し訳ありません)
|
原発に安全宣言が出されたらPCの組み立てを再開します。(G3)
|
|

原発の安全宣言を待ちたいところではあるが、早急に部屋を片付けなくてはならなくなり、10日振りに組立を再開した。作業机の上は3/11 PM2:46のママだった。

CPUクーラーファンの位置決めに手間取り、仕上げに2時間ほどかかった。このケースはビスナットのお化けのようなつくりの為、忘れ物をしたらタイヘン。ワッシャ1個でもショートの原因になる。何度も念入りに確認をしてからSW-ON。一発で無事起動した。直ちにWin7pro64 sp1にUpdateし、Event Viewerのログを確認した。特に問題はなさそうだ。

120mmのフロントファンと100mmのサイドファンは7V駆動、60mmのリアファン2個は5V駆動にしたので十分に静か。各部の温度は、CPU:30~32℃、HDD:26℃、M9120:38℃。電源スイッチは少し硬めだが確実感があって好ましい。 (室温22℃)
|
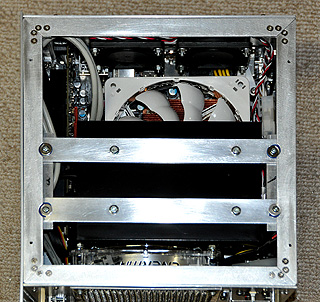 |
上面
ケースの奥行を数cm増すか、或いはフロントファンを小型化すれば、HDDはもう1台入る。
HDDの取り付けにゴムブッシュを使ったので、ケースに触っても振動は感じられない。
|
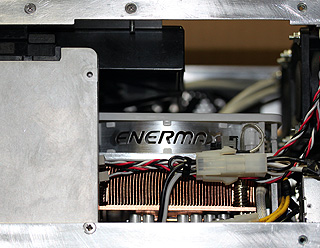 |
右側面
CPUクーラー・ファンとHDD消音ボックスとの間隔は23.5mm、CPUクーラーをSamuel17にすると、クリアランスは5.5mmになる計算。
|
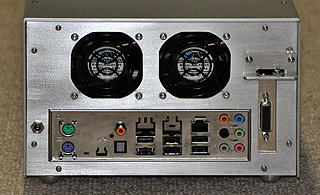 |
背面
クリアラッカー仕上げは、アルマイト加工に比べて格段に見劣りする。
フロントファンが充実しているので、2連60mmファンは5V駆動で十分。
|
|
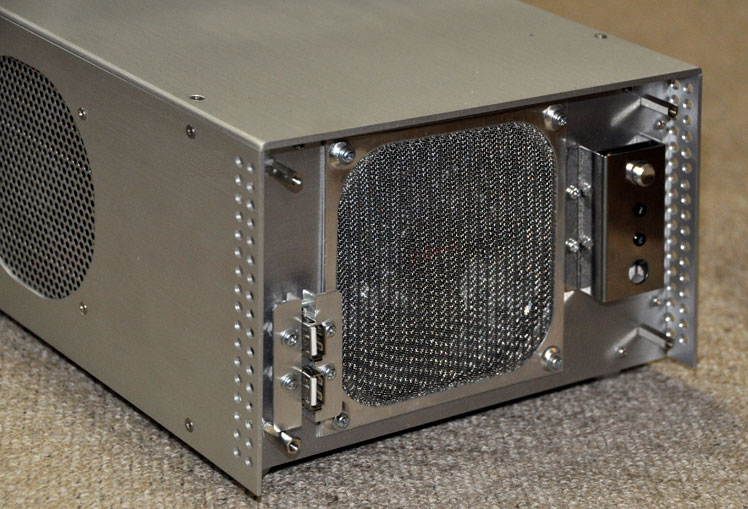 |
前面
天板と側板が少しずれているのは、寸法違いではなく側板の反りによる。100mファンの穴を仕上げる時、板を強く握り絞めてサンドペーパーを掛けたために歪めてしまった。中々上手く矯正できない。 取り付けビスを増やせば解決するのだが、今回は良い事にした。

吸気は左右の穴 (17個2列両側=68個の径4mm穴)、及び底面 (化粧パネルとの間隔は15mm)から。
フロントパネルはビス4個で簡単に着脱できる (手回し可)。
(化粧パネル付きの写真は3/9の節に)

次回は、もう一度ベンチマークテストを行う予定である。それまで、連続運転させよう・・・
|
|

仕上がったケースの仕様を確認しよう。製作途中で縦方向と奥行方向の寸法を変更したので、当初の予定より少し大きくなった。
自作PCケース1号機仕上り寸法
|
横方向 (左から)
|
|
|
縦方向 (下から)
|
|
側板の厚み
|
2
|
底板の厚み
|
2
|
パンチングメタルの厚み
|
1
|
M/Bを固定するスペーサーの高さ
|
10
|
サイドファン
|
12
|
M/Bの基板及び上方のクリアランス
|
84
|
ファンとビデオカードの間隔
|
3
|
2.5"HDD消音ボックスの厚み
|
25
|
ビデオカードがM/Bからはみ出る分
|
6
|
HDD消音ボックスと天板の間隔
|
8
|
M/B
|
170
|
天板の厚み
|
3
|
M/Bと側板の間隔
|
19
|
合 計
|
132
|
サイドファン (取り止め)
|
|
|
ファンガード (取り止め)
|
|
側板の厚み
|
2
|
合 計
|
215
|
|
奥行方向 (前から)
|
|
|
後板 縦方向 (下から)
|
|
フロントパネルの厚み
|
3
|
底板の厚み
|
2
|
フロントパネル2枚の間隔
|
15
|
M/Bを固定するスペーサーの高さ
|
10
|
フロント補助パネルの厚み
|
2
|
I/Oパネル
|
44
|
フロントファンの厚み
|
25
|
I/Oパネルとリアファンの間隔
|
7
|
フロントファンとM/Bの間隔
|
19
|
リアファン
|
60
|
M/B
|
170
|
リアファンと天板の間隔
|
6
|
M/Bとリアパネルの間隔
|
2
|
天板の厚み
|
3
|
リアパネルの厚み
|
2
|
合 計
|
132
|
合 計
|
238
|
|
|
|
ケースの寸法は、W215xH132xD238=6.75L
(縦方向に4mm、奥行方向に3mm増した)
|
|

では、反省点をまとめておこう。

・今回は三方向直角接合部分のアルミアングルを45度で合わせたが、微調整に相当手間取った。次回からは、二方向を45度、一方向を90度に設定する予定である。

・側板の厚みに迷った挙句、結局2mm厚にした。ファンの穴を空け、尚かつ折り曲げ処理ができない場合は3mm厚のアルミ板を使いたい。

・通常、M/B下の空間は6~7mmだが、今回は10mm確保した。余分なケーブル類を押し込むの好都合だった。そうなると通風についても配慮しなくてはならない。

・側板制作時、2.6mmのタップを立てるために2.2mmの下穴を空けるべき所を、誤って2.4mmの穴を空けてしまった。 そのまま2.6mmのタップを切ったらユルユルでダメ。 急遽カレイナットを使って収拾した。これは便利だ。

・皿ネジの頭を面位置にするためには面取り用のドリル刃が必要になる。今回は100個所以上の処理をしたため、途中で切れ味が劣化した。 ダイアモンドヤスリで研ぎ出したが、気付くのが遅く一部あまり美しくない穴もあった。次回は研ぐ頻度を上げよう。

・アルミ板の工作は精度が命。糸鋸盤の使い方を勉強し直そう。

結果は
【Windows Experience Index】 7.3 7.5 5.2 3.6 7.8
【3DMark06】 走らず
【Superπ104万桁】 13秒
【Yume1024×768最高】 3542 ← 書き間違いではない
【アイドル時消費電力】 43W
【Windows Experience Index計測時ピーク消費電力】 97W
【Full-HD TSファイルの再生】 良好
【Full-HD Flashの再生】 良好
|

自作PCケース1号機については、これにて一件落着とします。
足掛三年に亘る「P55-T36 + L3426」PCにお付き合い頂きましてありがとうございました。
|
一先ずおしましい
|